There’s nothing quite like the chemical industry. The world’s third largest industrial sector employs more than 10 million people and generates an incredibly broad range of products that impact every element of our lives. From industry to clothing, from food to healing people, manufactured chemicals have become intrinsic to our society.
Manipulating the very building blocks of the universe, the chemical industry is highly complex and often very hazardous for those involved. Workers in this industry must protect themselves against all kinds of risks. Chemicals can be toxic, invisible, corrosive, explosive or carcinogenic as well they reacting quickly or slowly. Chemicals can be absorbed inhaled, or projected which makes the health and safety demands in the sector among the highest in the world.
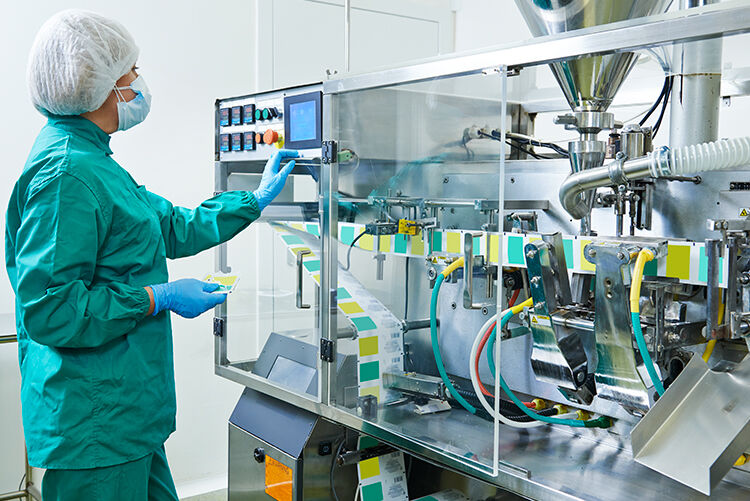
The Pharmaceutical Industry
One of the largest segments of the chemical sector is the pharmaceutical industry. Over 5 million people work in the pharmaceutical industry worldwide, according to an International Federation of Pharmaceutical Manufacturers & Associations (IFPMA) report in 2017. The report ‘Economic Impact of the Pharmaceutical Industry’ shows that almost 3.5 million of these workers are in Asia, almost three-quarters of a million are in Europe, and over a quarter of a million in North America.
The majority of employees work in high-tech research and development (R&D) labs or large-scale production facilities. In the US, for example, R&D employment represents 40% of the total direct employment within the sector. This is closely followed by pharmaceutical manufacturing, with 35% of the total employment base, according to the study by TEConomy Partners.
A HAZARDOUS WORKPLACE
Despite being one of the biggest employers in the world, the pharmaceutical industry is keeping significant occupational health hazard issues under wraps. Accurate figures on the frequency and severity of workplace injuries are hard to come by, raising suspicion in health and safety circles.
“Little is known about the health risks of working in the pharmaceutical industry. On the surface, the industry looks clean. The production of medicinals demands a carefully maintained and sterile
working environment and the white lab coats worn by workers add to the illusion of safety,” claim Bhusnure et al. in their 2018 paper entitled Chemical hazards and safety management in pharmaceutical industry.
“The appearances are deceptive, though producing drugs and other medicinals may involve exposure to toxic industrial chemicals. And while the finished products may be lifesaving medications for sick people, they can be dangerous to workers who are inhaling or absorbing them during the production process,” the paper continuous.
Hidden Risks
Working in environments where drugs are developed and manufactured put workers at high risk of coming into contact with dangerous substances. Often colorless and odorless, these invisible and potentially toxic substances can affect workers acutely, from one exposure, or chronically, from regular exposure. Airborne substances may be inhaled, where they can affect the lungs or enter the bloodstream.
“Direct contact of the skin and eyes by hazardous substances is another important route of exposure,” warns Bhusnure et al. (2018). “The eye is particularly vulnerable because airborne chemicals can dissolve in its moist surface and be carried to the rest of the body through the bloodstream (capillaries are very close to the surface of the eye).”
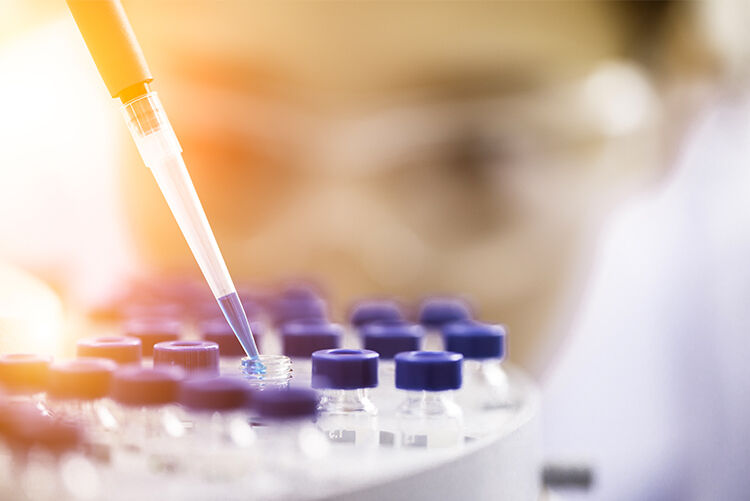
Protecting Workers
In the pharmaceutical industry, it is fundamental to maintain a protective barrier around the worker while in environments where dangerous substances are present. Wearing protective eyewear is just one element for keeping the eyes safe from chemicals in pharmaceutical environments. Workers are advised to minimize contact with liquid and solid chemicals and also keep their hands away from the face until they are sterilized. Workers should also avoid wearing contact lenses as they may trap chemicals against the eye surface.
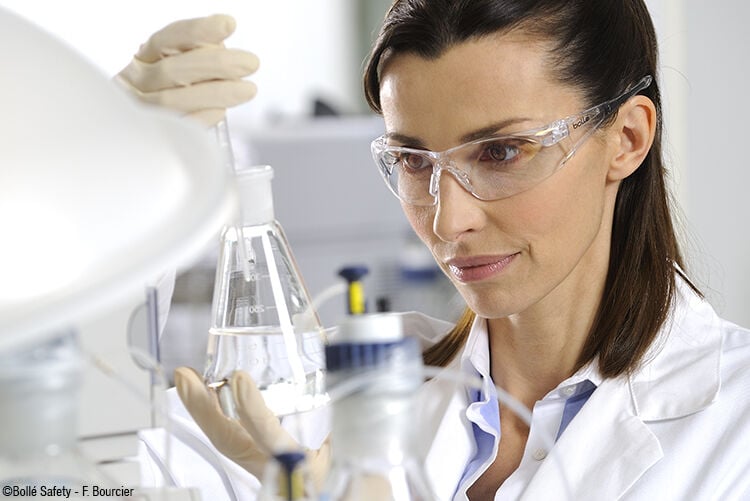
THE IMPORTANCE OF STERILE ENVIRONMENTS
"CREATING A BARRIER BETWEEN THE WORKERS AND THE PHARMACEUTICAL ENVIRONMENT IS NOT JUST ABOUT PROTECTING PEOPLE BUT ALSO THE PRODUCT"
Creating a barrier between the workers and the pharmaceutical environment is not just about protecting people but also the product. For most drugs, vitamins and other pharmaceutical products, it is essential to avoid contamination. That includes human skin, hair, eyelashes or bodily fluids that may be carrying germs, bacteria or other potentially harmful substances.
“People are the biggest source of potential contamination to a sterile cleanroom, so sterile clothing is crucial. As a basic requirement, sterile clothing must help maintain a cleanroom’s cleanliness while people are working in the area, by ensuring that particle and microbiological levels are kept below the limits for the chosen grade of the area,” says Jaime Cassar, cleanroom category manager at Kimberly-Clark Professional Europe.
In many pharmaceutical environments, protecting the product from the worker is often a higher priority than protecting the worker from the product. Some drugs may have limited harmful effects on the worker but one cough or sneeze could make an entire batch of products unsafe to sell. Therefore, creating a barrier between the worker and the product could save millions of dollars in lost production.
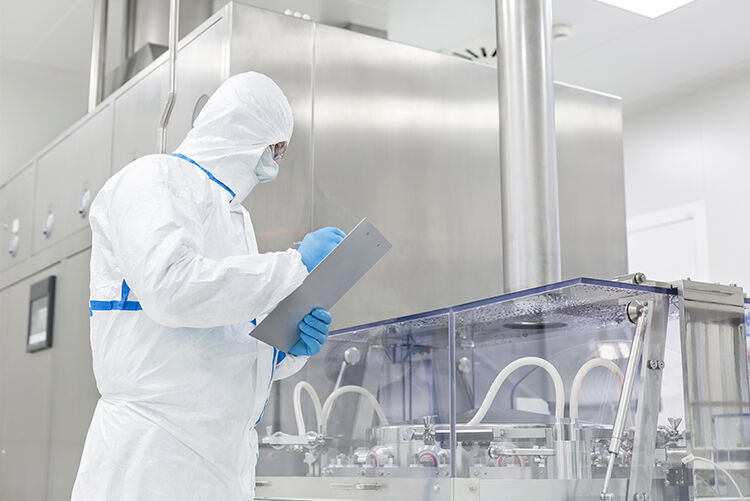
Cleanrooms
ISO 14644-1:2015, the international standard on cleanrooms and associated controlled environments, defines the regulations for these environments. They define a clean room as: “a room where the concentration of airborne particles is controlled, and which is constructed and used to minimize the introduction, generation and retention of particles inside the room and in which other relevant parameters such as temperature, humidity and pressure are controlled as necessary.”
The primary function of a pharmaceutical cleanroom is to protect the product from contamination. For pharmaceutical manufacturers, the effectiveness of cleanrooms can be the difference between success and failure, as ineffective cleanrooms undermine the safety of the product. As such it is essential for pharmaceutical companies to address all potential sources of contamination, which includes the workers themselves.
PPE FOR THE PHARMACEUTICAL INDUSTRY
"EMPLOYEES WORKING IN PHARMA INDUSTRIES OFTEN ENCOUNTER LIFE-THREATENING RISKS AS THEY CONTINUOUSLY HAVE TO DEAL WITH HARMFUL CHEMICAL SUBSTANCES AND DRUGS"
Personal Protective Equipment (PPE) is used to create a barrier between people and products in pharmaceutical development and production environments. This equipment must protect workers from the wide range of hazards posed but also keep these sterile environments free from contamination by workers. PPE should also offer comfort and mobility as well as the means to see and breathe, so workers can carry out their work effectively.
“Employees working in pharma industries often encounter life-threatening risks as they continuously have to deal with harmful chemical substances and drugs. This is especially true in case of cytotoxic drugs that are highly effective to treat diseases, but are toxic enough to pose a dangerous health risk to health care professionals, pharmacists, nurses, and manufacturers who handle them,” explains a 2017 review by GM Insights.
“PPE thus, helps provide security to workers from harmful biological and chemical substances including infective agents,” continues the review. “It should be remembered that while selecting the right PPE, factors such as the contamination type and application type need to be considered. However, while donning and choosing the correct PPE for the pharmaceutical unit, the key aspects to be taken into consideration include comfort, quality, microbiological protection, regulatory compliance with norms and standards, and product cost.”

Types of PPE
PPE is the final line of defense when it comes to protecting personnel from these potentially toxic substances. Bodysuits, gloves, goggles, and boots must all be designed and made using materials that protect the worker and the products. Meaning they must block harmful substances coming into contact with the worker, while also keeping human elements or material fibers from reaching the product.
All these types of PPE must protect against particle intrusion, for example. The Type 5 test is commonly used to specify the minimum requirements for chemical protective clothing resistant to penetration by airborne solid particles. During this 9 minute test, sodium chloride particles at 0.6 micron size are sprayed at the sealed equipment. In order to pass this test, 80% of equipment must have, on average, less than 15% leakage.
Protective eyewear must adhere to even higher standards of protection. The eye is vulnerable to harm from a variety of substances present in the pharmaceutical environment because it provides a direct route to the bloodstream. Therefore, protective eyewear for the pharmaceutical industry must be resistant to particles, chemicals, temperature, light, and be autoclavable for sterilization.
Eyewear Standards in Pharmaceutical Environments
The wide range of hazards posed by the pharmaceutical environment require the highest standards of safety eyewear. Goggles and glasses should be able to withstand impact, bright light, corrosive substances, and offer reusable solutions that prevent contamination.
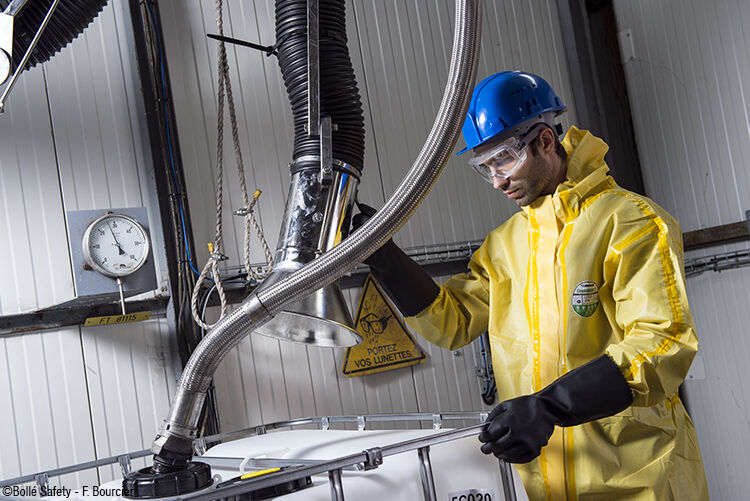
- Autoclavable
An autoclave is a sterilization process involving steam at temperatures between 121 and 134 degrees Celsius. Autoclave sterilization is required for the reuse of equipment in cleanrooms and other sterile environments. While using autoclavable goggles, for example, pharmaceutical companies can maintain sterile spaces while removing the financial and environmental cost of single-use equipment.
- Physical Damage
The EN166 standard guaranteed minimum resistance of the protective eyewear against everyday risks including dropping the protective eyewear onto the ground, aging by light exposure, heat exposure or corrosion, for example. EN166 also has a K option, offering resistance to surface damage by fine particles using an anti-scratch coating, and an N option for anti-fog coating.
- Chemical Risk
Environments with chemical risk level 3, require eye protection against liquid droplets or splashes. While a risk level 4, requires eye protection against large dust particles smaller than 5 microns. Goggles, adapted spectacles with strap or face shield are mandatory in these common pharmaceutical environments.
- Mechanical Risk
The B classification for environments with potential mechanical hazards refers to the risk of medium energy impacts when eyewear should resist a 6 mm, 0.86 g ball fired at 120 m/s. The T classification refers to high-speed particles at extreme temperatures, which are also common in the pharmaceutical industry.
- Harmful Light
The EN170 standard offers protection against ultraviolet radiation. This type of protection is particularly recommended during activities where the source of ultraviolet radiation is predominant, such as mercury vapor lamps, actinic or germicides.
ONLY THE BEST WILL DO
The eyes represent one of the most important parts of the body to protect within the pharmaceutical environment. They are vulnerable to a range of hazards present in the sector and fundamental to vision, which in turn allows employees to carry out their work, stay safe and ensure the integrity of the product. When it comes to safety eyewear in the pharmaceutical industry, only the highest standards will do.